A Technical Primer for Systems Integrators and Operators
By Aaron Steiner and Eric Chapman, Image Credits: Mark Whelan
As seen in Sea Technology
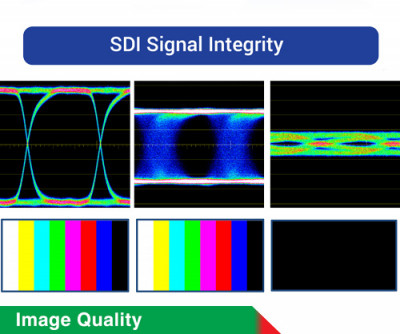
For digital video, such as HD-SDI, received video quality
is unaffected by signal quality as long as the data are recoverable.
Through advancements in technology, the tools to explore and work in the depths of the seas have brought humanity closer and closer to these spaces. Remote video technology, which has become ubiquitous in the subsea industry, is among the key technologies which has enabled humans to effectively explore the oceans and operate vehicles at depths beyond the practical reach for manned missions. High definition (HD) video solutions offer a substantially higher quality of information than previous video technologies, and enable operators to make better decisions and to operate more effectively. Along with improved quality, HD video presents new challenges for operators and system integrators at nearly every level of the subsea imaging system. Understanding how these challenges affect the system is key to maximizing the benefits HD video can offer.
Pixel Size Matters
The term “High Definition” refers specifically to the resolution of an image – for a given optical format of image sensor, higher resolutions are achieved by dividing the image sensor area into more, smaller, individual sensing areas or pixels. Typical image sensors operate on the same basic technologies regardless of their resolution and as a result have very similar performance per unit area. The reduced sensing area of smaller pixels results in proportionally reduced light sensitivity and poorer signal to noise ratio compared to the larger pixels of an equivalent size but lower resolution sensor.
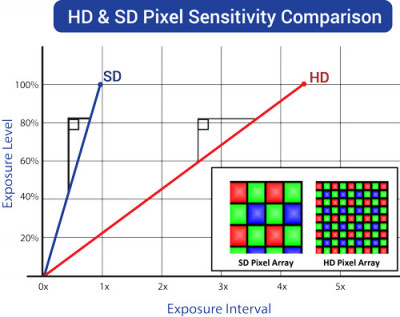
Comparison between the pixel-level sensitivity of example
one-third-inch-class standard-defnition and high-defnition
video sensors. The slope is proportional to sensitivity.
If a typical 1/3-inch class standard definition imager is used as the basis of comparison, it’s array of 6.35 x 7.40 micrometer pixels produces a low noise, well exposed image with 1 Lux of scene illumination. For the same exposure target, a high definition imager in the same 1/3-inch class with an array of 2.8 x 2.8 micrometer pixels requires more than four times as much scene illumination or proportionally longer shutter speeds. Shutter speeds can only be reduced so far before reaching the frame refresh rate of the video system – typically between 1/25th and 1/60th of a second. Once the frame refresh rate limit is reached the sensor produces underexposed images and/or noisier images as the camera increases its internal signal gain.
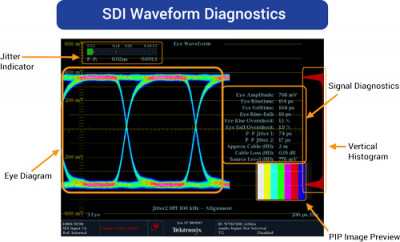
Example of an HD-SDI video diagnostics screen from a Tektronix
WVR-7200 broadcast waveform analyzer. (Image Credit: Mark Whelan)
Overcoming the inherent sensitivity limitation of high definition imagers therefore requires shutter speeds longer than the video frame rate, larger format image sensors with larger pixels, and/or more light. While many high definition cameras are capable of shutter speeds below the video frame rate, the resulting images are undesirable for operator-in-the-loop applications such as Remotely Operated Vehicle (ROV) piloting or manipulator work. The resulting slow image refresh rate appears choppy and contributes to latency. Larger format imagers have their place in primary science and piloting cameras, but have limited utility on smaller vehicles and in tight spaces. The large format high definition sensors used in this class of camera also drive up the cost, size, and complexity of the camera while reducing depth of field.
A higher priority on lighting, e.g. providing higher scene illumination, even light distribution, and scaleable output, creates a more versatile and robust HD imaging platform and frees system designers to use a broader range of imaging devices. Lighting design is a cornerstone of subsea imaging and using flexible and capable lighting installations enables successful operation in a wider range of conditions. Modern subsea LED lights, such as the DeepSea Power & Light SeaLite Sphere, enable operators to control light output dynamically and offer space efficient form-factors which ease integration for system designers.
More Pixels, Higher Bandwidth
The high pixel in count HD imagers impacts more than just the camera selection and lighting aspects of subsea imaging. High resolution video inherently contains more image data than standard definition video and consequently requires higher bandwidth signals. For comparison, standard definition composite analog video utilizes less than 6 megahertz of bandwidth, whereas 4K Ultra HD Serial Digital Interface (SDI, a broadcast video standard) requires 6 gigahertz of bandwidth: a 1000x increase.
Transmitting HD video signals at speeds ranging from a few hundred to a few thousand megahertz through subsea cables and connectors presents challenges. The electrical characteristics of many conventional subsea cables and connectors can look like a wall to high bandwidth signals and effectively block their transmission. These high speed signals require specialized connectors and cables with highly tuned electro-mechanical properties and matched characteristic impedances in order to maintain signal integrity at depth.
Maintaining signal integrity from the video source at depth to the top-side distribution and recording equipment is critical at every link in the video transmission chain. The two basic classes of on vehicle high bandwidth interconnects are: 1) impedance controlled copper, or 2) fiber optic.
High Bandwidth Interconnects
The most common controlled impedance copper solutions are either twisted pair Ethernet type interconnects, or coaxial. Ethernet is widely used in subsea imaging, including sonars and other acoustic imaging equipment, and the established interconnect solutions are field proven. Depending on the bandwidth requirement of the digital data and the electrical characteristics of the interconnects, the maximum transmission distances for Ethernet may range from 10 to over 100 meters. Many variables impact maximum transmission distances and achievable data rates so validation and testing are key for any copper based high bandwidth connections.
The HD-SDI video standard evolved to fulfill the needs of the broadcast industry. Because of the standard’s heritage, HD-SDI hardware is designed around 75 ohm coaxial infrastructure much like analog video distribution systems. With the available subsea coaxial connectors, standard HD-SDI signals can reliably extend to around 10 meters. Using specialized receivers, transmission distances can be extended, however the practical limit is still only measured in the tens of meters. For cable runs longer than those required for on-vehicle interconnects fiber optics are the best solution.
In deep water and remote applications fiber optic connections are the only reliable way to transmit high bandwidth signals over ROV tethers or tie-back cables up to many tens of kilometers. Fiber interconnects are gaining acceptance in the short runs for on-vehicle connections as well. In ROV applications, because these signals are sent over fiber through the vehicle tether, starting with an optical signal eliminates the need for additional upstream copper-to-optical conversion. There are challenges associated with fiber regarding the robustness of the cabling and interconnects, especially for on vehicle use, but these can often be mitigated through careful cable management.
New technologies from the professional and consumer electronics markets continually expand what is possible in subsea imaging applications. Real-time video compression is becoming common in the broadcast and surveillance markets and technology transfer to subsea applications will result in lower bandwidth requirements and longer transmission distances over copper interconnects. At the same time, use of even higher resolution video formats are expanding in other industries and will eventually see adoption within the subsea industry. Fiber offers the most future proof solution for high bandwidth signal transmission, however each interconnect class has its merits and, depending on the specific application, either one may be preferred.
Digital vs. Analog
In contrast with analog composite video or component video, most high definition video standards are based on digital signal transmissions. HD-SDI, GigE Vision, and Internet Protocol – Real Time Protocol (IP-RTP) are among the most common digital video standards found in subsea applications.
Power supply noise, signal attenuation, and cable reflections all degrade image information transmitted over analog video formats. The susceptibility of analog video to noise is rooted in the time and amplitude encoding of the image information. Any interference that changes the signal timing or amplitude directly affects the picture. With digital video, as long as the binary bit pattern can be reconstructed, the original image information can be perfectly reproduced. This is why subjective image quality in analog video gradually transitions from good to bad as the signal-to-noise ratio decreases, whereas with digital video the transition from good to bad is nearly a step function: it either works or it does not.
The degradation of analog video caused by interference or attenuation is certainly a disadvantage, however, skilled technicians are frequently able to troubleshoot basic problems just by viewing the image. In contrast, the image data contained in digital video is typically unaltered by a degraded signal. In order to see potential issues or to diagnose the causes of signal loss, technicians require specialized equipment such as broadcast waveform analyzers for HD-SDI video or packet and protocol analyzers for Ethernet systems. These analyzers have the capability to inspect the digital video data at both the electrical level and the bit level, exposing signal integrity issues such as timing errors or amplitude attenuation as well as bit errors and packet format errors.
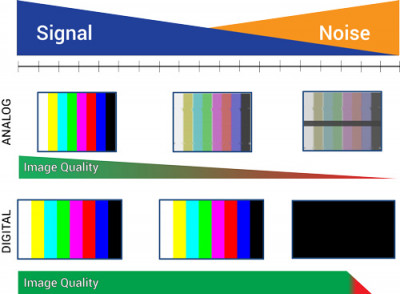
Analog video quality degrades as signal to noise ratio drops whereas digital video quality remains high then drops suddenly.
High speed transmission technologies in the broadcast and telecommunications industries have driven the need for not only the equipment necessary to analyze and qualify digital video standards, but also the technology to reliably recover and recondition degraded data streams. For instance, in HD-SDI applications cable equalization techniques and reclocker circuits allow lossless recovery of the original image data from a degraded signal. Recovering and restoring the original image data is a unique advantage of digital video signals, and incorporating these restoration technologies at all receiving interfaces is consistent with best practices.
The drive for high performance HD imaging solutions for the subsea industry highlights the need for ever better access to some of the most remote and harshest environments on Earth. HD video technologies bring a fuller and more immersive visual context to demanding remote subsea operations and provide higher quality feedback and information to users. The applications for HD video are expanding into the tooling and wide-angle context camera space with products like the unique DeepSea Power & Light HD Multi SeaCam. These and similar innovations continue to expand the capabilities of subsea imaging into new and uncharted depths.